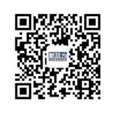
微信公眾號二維碼

微信咨詢顧問二維碼
新益為5S咨詢公司概述:大多 數企業在安全管理上的主要措施仍然是經濟措施和強制手段,稍有放松,事故就會反彈。為什么會出現這種情況?為什么企業的千人負傷率在達到0、5—— 1%之后就很難再有大的突破?如何破解當前企業安全管理遇到的瓶頸和難題?精益安全的理念和方法試圖在這些方面進行一系列有效的探索。
精益安全管理
那么,精益安全的理念和方法與傳統安全管理有什么不同呢?
1、精益安全管理是“走群眾路線”
安全工作是為了誰?是為了領導?還是為了員工?這里有一個關于“三滿意”的排序問題。在傳統安全管理中,多數人的工作方式是按照工作計劃、根據領導的要求去工作,完成領導交辦的任務,讓領導滿意。
“三滿意”的排序是“領導一客戶一員工”,員工被排在了最后面。員工不滿意,員工在心里不痛快,在產品上就會體現出來,產品性能不穩定,客戶就會有意見,丟失了市場份額,企業的效益下滑,領導會很不高興。這就是在很多企業不斷循環的“管理怪圈”。產生“管理怪圈”的根源是因為管理者的行為與安全的目的“相悖而行”。
要讓管理者的行為與目的“相向而行”,就是精益安全管理主張的“走群眾路線”。領導干部到現場去,聽取員工的意見,解決員工在生產和工作中的困難,關心群眾、熱愛群眾、一切為了群眾,“三滿意”的排序是“員工一客戶一領導”。
2、精益安全管理是“把好鋼用在刀刃兒上”
精益安全管理主張“素質低,不是員工的錯”,“管理者,首先是培訓師”。有效控制事故的發生,就要把不斷提高員工的安全素質和安全能力放在重要的位置,建立內訓師隊伍,加強對一線員工的培訓,“把好鋼用在刀刃上”。傳統安全管理只注重中高層領導的培訓,領導的能力提升以后不去培訓員工,員工的安全能力得不到加強,等于“把好鋼用在了刀背兒上”,解決不了安全生產的現實問題。
3、精益安全管理是“現場思維”
精益安全管理主張“現地、現物”和現場主義。認為:問題發生在現場,分析問題、調查研究問題和解決問題也應該在現場。我們稱之為“現場思維”。只有身臨現場,才能體驗到員工在生產作業時的真實環境和真實感受,才能了解到真實情況。管理者 把資源用在了現場,準確地把握了事故隱患是在什么時間、什么地方、什么情況下、是誰在操作時發生的。制定出來的防范措施才更有效、更有針對性。
4、精益安全管理是“基于過程的管理”
精益安全管理是“基于過程的管理”。所謂“基于過程”,實質上是考察生產現場、作業流程和員工行為符合標準的程度,著眼于生產秩序、設備運行和質量控制的穩定性以及關注作業現場4M1E的受控情況。過程控制的指標包括:現場3S狀況、員工參與率、改善提案件數、崗位點檢執行率、現場隱患舉報件數、行為觀察次數、員干離職率等;實現過程控制的措施有:ANDON安全行為模型、自慟化、防呆防錯、看板管理、確認制等等。
5、精益安全管理是“回歸人的本性”
在豐田的班組有一項活動叫“安全日歷活動”,每天工作結束以后,每一位員工都要進行當日安全自省,要自我反省三件事:①“班前會上指出的安全重點落實了嗎?”②“3S執行了嗎?”③“被別人指出不安全行為了嗎?”通過自我檢點,自己給自己打分。如果因為自己的失誤給全班帶來了麻煩,自己會感到很內疚和恥辱。
通過一系列自主管理的方法,激發員工的內生活力,通過主動關愛和現場改善活動,實現安全管理的自覺、自愿、自主管理。千方百計讓員工在作業的時候動腦筋。很多事情,當你換一種方法去處理的時候,情況就大不一樣了。
6、精益安全管理“注重重復性活動”
精益安全管理不排除進行有意義的一次性活動, 但相比較而言,更注重扎扎實實地開展日常工作不可缺少的重復性活動。這些活動大多不用加班加點,只要用心去做、做到位、全員參與、堅持做下去,其效果往往就會出人意料。像原日本鋼管公司京濱制鐵所5S活動管理持續推進10 年,上海通 用汽車班組安全分享堅持了7年,美國一家氧化鋁提煉廠堅持安全行為觀察流程6年時間,安全管理都取得了優異的業績。
7、精益安全管理是“凡事皆要可測量”
精益安全管理針對這些病癥開了一劑藥方:“凡事皆要可測量”比如,廠長如何參與安全管理?精益安全開出的藥方是:“安全思路+1111安全行動方案”。廠長安全工作思路的測量點是
“您是否準確把握了本單位安全工作的三個點”;安全行動方案的測量點是“每個月使用 7 個小時做好以下4件事情:①每月1次安全行為觀察,30分鐘:②每月1 次帶隊安全綜合大檢查,120分鐘:③每月1次安全工作例會,90分鐘;④每月舉行1次面對4個班次員工的廠長安全講話,4個45分鐘。”有了這樣一些具體的、可操作、可測量的行動方案,很多理念、原則和要求就容易落地,就可以到位了。以上談了精益安全與傳
建立生產有序、管理順暢,操作規范,士氣高昂、高質量、低成本、短交期的作業現場;
為企業規劃設計一套由內到外的形象升級,外觀視覺價值體現、內在的管理內涵體現;
全員參與設備管理高產出和低成本運營,提升設備管理能力,維護能力,提高效率
構建班組生產管理體系、循環評價、人才育成、持續改善、績效管理、文化養成體系;
提高產品質量、降低生產成本、縮短交期、增加利潤,讓管理更系統科學,執行力更強
對工廠的各個組成部分進行合理安排,以提高生產效率、降低成本、優化物流、改善工作環境等